THERMOFORMING: MACHINERY FOR THERMOFORMING, BLISTER, SHEET AND FILM EXTRUSION FOR PACKAGING
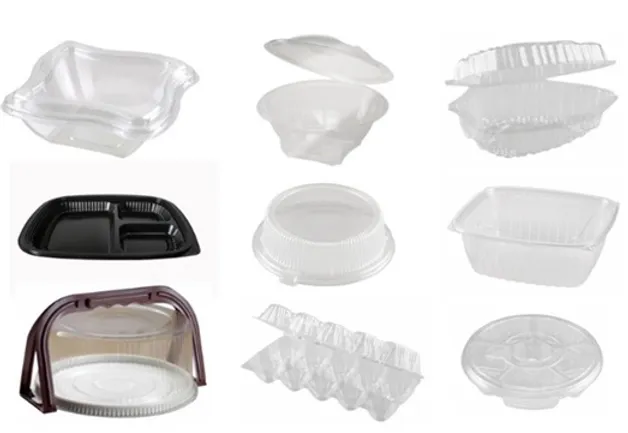
Thermoforming or thermoforming is a process consisting of heating a semi-finished thermoplastic plate or sheet, so that when it softens it can adapt to the shape of a mold by vacuum pressure action or by means of a countermould. Thermoforming is a process that consists of giving forms a plastic sheet by means of heat (120 ºC to 180 ºC) and vacuum (600 to 760 mmHg) using a mold or matrix (wood, epoxy resin or aluminum).
An excess of temperature can “melt” the sheet and the lack of heat or poor vacuum quality will result in a defective piece without defined details. Unlike other processes such as injection, blow molding and rotational molding, thermoforming is part of a rigid sheet of uniform thickness made by the extrusion process, and allows small productions due to its low cost in tooling, becoming profitable in high productions as well.
The most used materials are PAI, PP, PSI, PET, ABS, PEAD, PVC. It can also thermoform foamed PVC, polycarbonate, acrylic, etc. The most common thicknesses range from 0.2 mm (disposable containers) to 6 mm or more (casings for machinery). A characteristic restriction of this process is that the part to be thermoformed must be easily “unmoldable”, this means that the matrix must be wider at the base and narrower at the top.
This is commonly called the demolding or outlet angle and is generally at least 5 degreesStagesHeating of the semi-finished product, either by radiation, contact or convention.Moulding of the semi-finished product, which after heating is stretched adapting to the mold by means of different processes (pressure, vacuum, pressure and vacuum or a countermould). Cooling of the product, which begins when the thermoplastic comes into contact with the mold and is cooled by a fan or at room temperature and ends when the temperature is adequate to unmold the part without deforming it.
ParametersFurthermore, in this plastic transformation technique, a series of parameters must always be taken into account, which are: Forming temperature, which depends above all on the material to be transformed, but also on the complexity and thickness of the piece. Heating time, which depends above all on the thickness of the material, but also on its transmission coefficient.
This is of great importance, and must be sufficient so that the sheet reaches the forming temperature uniformly in surface and thickness. Cooling time, which depends on the same factors as the heating time, and must be sufficient so that the The final product is resistant and does not deform when demoulding. Pressure or vacuum, depends above all on the thickness of the sheet but also on the complexity of the piece. It must be controlled, since if it is insufficient, not all the details will be obtained and if it is excessive, holes or marks can be produced.
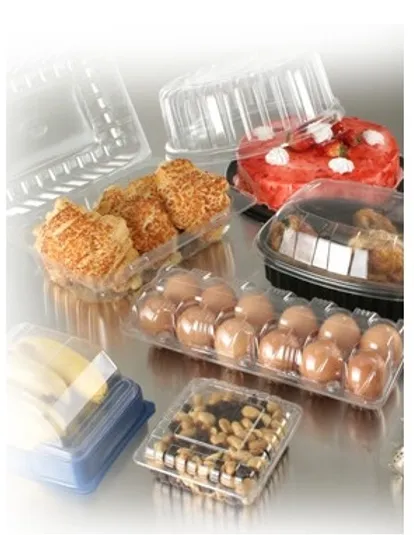