MACHINERY FOR BAG MANUFACTURING; BAGGERS; BAG SEALERS AND FLEXO PRINTERS
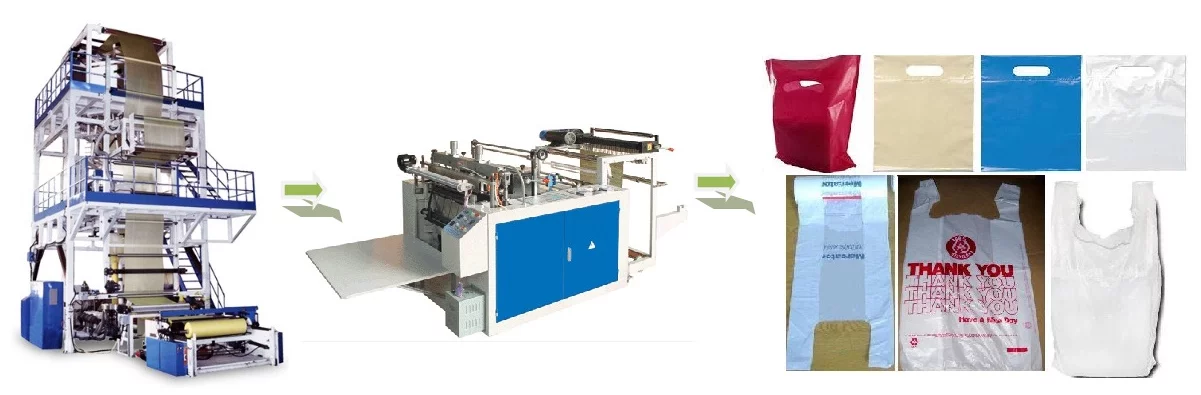
EXTRUSION BLOWN FILM
One of the most common methods of film manufacturing is blown film extrusion (also known as Tubular Film). The process involves the extrusion of plastics through a die, followed by bubble-type expansion. The main advantages of making film by this process include:
– Produce the tube in a single operation.
– Regulate the width and thickness of the film by controlling the volume of air in the bubble, the output of the extruder and the speed of the screw.
– Eliminate end effects such as edge shear and non-uniform temperature that can result from flat die film extrusion
– Biaxial orientation capacity (allowing uniformity of mechanical properties).
The blown film process contains the following elements:
– Extruder/Screw
– Adapter/Matrix
– Air ring
– Stabilization and Collapse
– Winding or bag making
EXTRUDER/SCREW
The extruder represents the backbone of the blown film process. The extruder is made up of a motor, a barrel with heating/cooling zones, and a rotating screw to drive the polymer into the extruder, melt the polymer, and then develop sufficient pressure to push the molten polymer through the die.
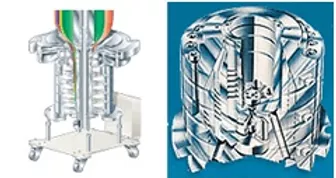
In the previous figure we can see diagrams of the cross section of extrusion blown film dies. Each layer is shown in a different color. The dies are manufactured with great precision and as expensive as they are, they have a considerable shelf life. Each die head will have a working range of different diameter die inserts to fit as the application requires. Different die openings can also be specified depending on the material to be used.
ADAPTER/MATRIX
The blown film die shapes the molten polymer exiting the extruder into an annular shape. The die is designed to provide a uniform velocity to the polymer around the circumference of the die outlet.
AIR RING
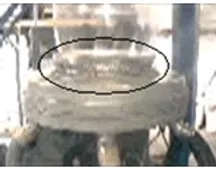
Once the molten polymer leaves the die, it takes on its final dimensions and cools. Stretching the molten polymer by expanding the bubble with air pressure inside and pulling the fabric down with nip rolls reduces the film to the desired thickness. Air exits through an air ring on the surface of the bubble to provide cooling for the molten polymer fabric, which is shown in the figure above.
STABILIZATION AND COLLAPSE
Once the molten polymer solidifies, the tube is stabilized and directed to a screen below the nip rolls.
After being transformed into a flat fabric, any of the auxiliary processes can be developed, such as: treating, cutting, sealing or printing.
WINDING OR MANUFACTURING OF BAGS
The finished film can be made into rolls using a winder for further processing, or it can be connected to an in-line machine and made into bags.
FLEXOGRAPHY PRINTING
For large print runs from coil, the most economical method is flexography. The printing is done from a flexible elastomeric sheet on which a photochemical attack is made from a negative (for each color) in the areas unprotected by it, so that its thickness is reduced and the image remains in relief. .
This printing method is a form of relief printing. The areas of the image that are raised are inked and transferred directly to the substrate. The method is characterized by having flexible plates made of a soft rubber or plastic and using fast-drying inks. Flexographic inks are particularly suitable for printing on a wide variety of materials, such as acetate, polyester, polyethylene, newsprint, among others.
The sheet is mounted on a roll over which film passes, which is fed with ink by contact with a series of rolls, the lowest of which is partially submerged in the ink bath. An upper roller ensures the contact of the film on the sheet, which transfers the film to it, which dries or polymerizes next.
For each additional color, another station with the same elements is needed. However, the relatively cheap cost of flexible sheets makes flexography the cheapest and most widely used method for medium to large runs.
CUT/REWIND
This process basically consists of two stages, in the first, the printed film is cut to give it the measurements required by the client and then the film is wound with the new measurements, then the cutting process is shown and the re- coiled
SEALING BY HEAT WITH ELECTRICAL RESISTANCES
There are several methods or procedures for making bags, the most used and well-known is sealing
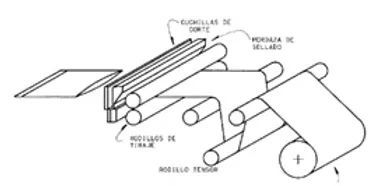
at the bottom of the tubular film where the tubular sheet of the roll is first stretched through pull rollers until the film is placed in the part of the machine, where the sealing will be done, once the bag is sealed it will be cut by knives .
In this type of bags there is only one seal that will be made across the width of the film. (Transverse seal) which is shown below.
SEALING BY HEAT WITH ELECTRICAL RESISTANCES
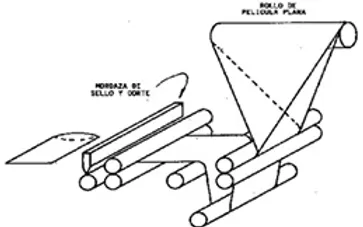
There is another type of bag used continuously and that differs from the previous one because the seal is laterally (side weld). Its elaboration can be done starting from the flat film, which is folded in half and sealed transversally at the same time that it is cut and separated. .
The side sealing system can also use tubular film in roll, which is cut in the same process to obtain two bags simultaneously in each cycle.
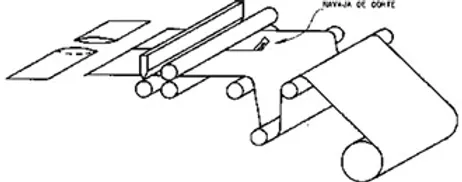
Typical applications (3-layer mono extrusion and co-extrusion lines):
• | High transparency films for stand-up pouches, twist-wrap packaging, automatic packaging; |
• | Films for subsequent laminating, coating, printing and other conversion processes; |
• | Heat-shrinkable films (“shrink”) and of the “stretch” type; |
• | Films for promotional bags”, “T-shirts”, garbage bags and others; |
• | Films for packaging paper towels and fabrics; |
• | Films for heavy-duty packaging, suitable for FFS (Form & Fill, Seal-Film) systems. |
Parameters:
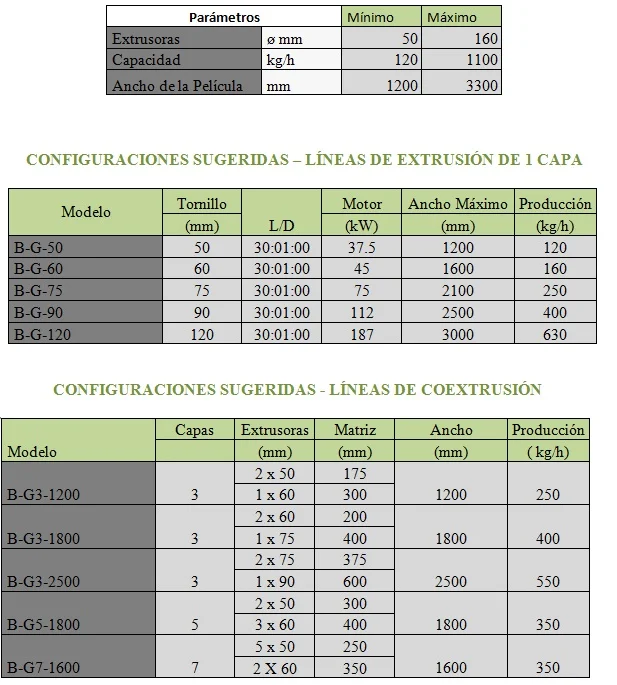